Leibniz-Institut für Verbundwerkstoffe: Erforschung zukünftiger Anwendungen von Verbundwerkstoffen
Um die CO2-Bilanz eines Unternehmens zu verbessern und damit den ausgeweiteten Umwelt- und Klimaschutzregelungen gerecht werden zu können, sind häufig nicht nur neue Technologien, Prozesse und Produkte, sondern auch neue Werkstoffe notwendig. Der Wechsel zu innovativen, leichten Verbundwerkstoffen ermöglicht gleichzeitig eine entsprechende Reduktion des CO2-Footprints und die Optimierung der benötigten Bauteileigenschaften. In diesem Bereich ist das Leibniz-Institut für Verbundwerkstoffe (IVW) in Kaiserslautern tätig.
Die Forschungseinrichtung entwickelt in ihren Forschungsprojekten und Industrie-Kooperationen basierend auf wissenschaftlichen Grundlagen maßgeschneiderte Werkstoffe, Bauweisen, Fertigungsprozesse und Prototypen. Die Lösungen des IVWs finden unter anderem in den Branchen Automotive, Luft- und Raumfahrt, Maschinenbau, Medizin und Energie Anwendung.
Auch im Bereich der Kreislaufwirtschaft unterstützt das Leibniz-Institut für Verbundwerkstoffe seine Partner bei den Fragestellungen:
• Wie können End-of-Life-Komponenten in gleichbleibender Qualität in neuen hochwertigen Anwendungen eingesetzt werden?
• Wo können nachhaltige Materialien in Verbundwerkstoffen optimal eingesetzt werden und einen Mehrwert schaffen?
Im Luftfahrtbereich entwickelt das IVW in einer Kooperation mit AIRBUS einen neuen Fertigungsprozess zum Recycling von Hochleistungsverbundwerkstoffen, die durch ihr geringes Gewicht eine Reduktion des Treibstoffverbrauchs ermöglichen. Der neue AIRBUS A350XWB besteht zu über 50 % aus kohlenstofffaserverstärkten Kunststoffen. Zusätzlich zur Wiederverwertung der wertvollen Werkstoffe nach der Nutzungszeit eines Flugzeugs kann auch das Recycling der Produktionsabfälle zur Umweltschonung und Kostenreduktion genutzt werden.
Im Automotive-Bereich erfolgt im Rahmen des Verbundprojekts NeuRecA sowohl für Kohlenstofffaser-Produktionsabfälle (Verschnitt von Textilien und Spulenreste) als auch für recycelte und aufbereitete Kohlenstofffasern von End-of-Life-Bauteilen eine zielgerichtete Materialentwicklung zur Wiederverwendung in neuen Bauteilen. Hierdurch kann der ökologische Fußabdruck von kohlenstofffaserverstärkten Bauteilen deutlich gesenkt und die Attraktivität des Werkstoffs weiter gesteigert werden. Zur Fertigung dieser Halbzeuge wird das Sheet Molding Compound (SMC)-Verfahren genutzt, da es eine hohe Designfreiheit bei gleichzeitig wirtschaftlichen und effizienten Fertigungsprozessen ermöglicht. In Kombination mit einem Epoxidharz werden so SMC-Halbzeuge entwickelt, welche in thermisch hochbelasteten, strukturellen Bereichen eingesetzt werden können.
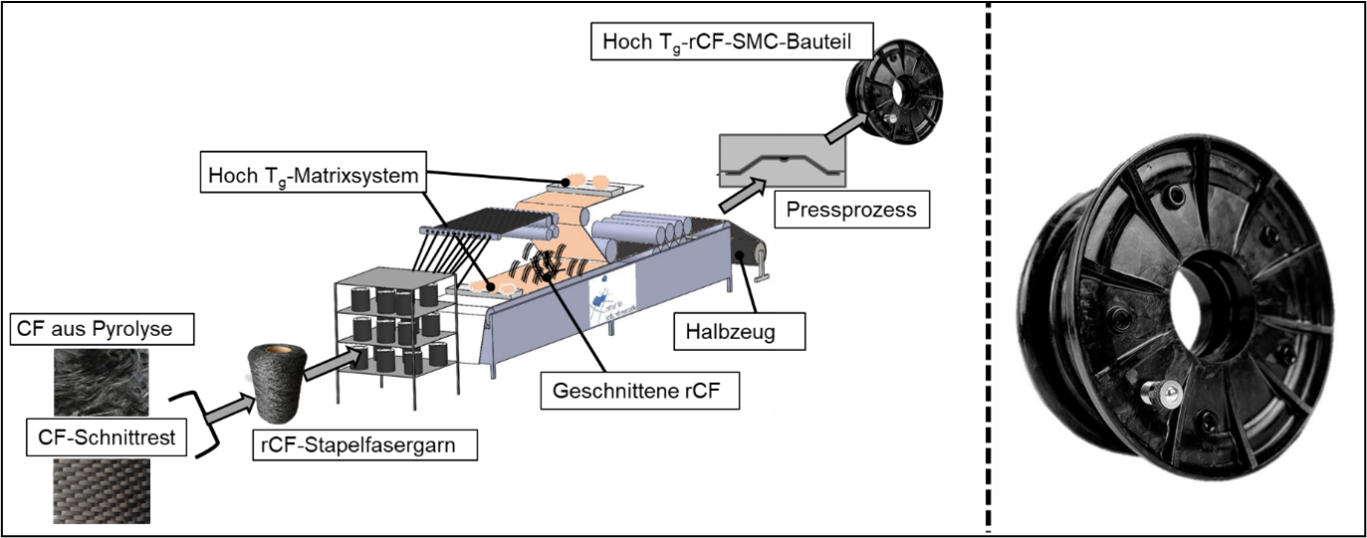
Abbildung 1: NeuRecA: Schematisch vereinfachte Prozesskette zur Herstellung des neuartigen SMC auf Basis von rCF (links) und aus SMC gefertigte Felge der Blackwave GmbH (rechts)
Im Bereich der Nutzfahrzeugbranche befasst sich das IVW im Projekt drivEcomp II mit der Steigerung der Energieeffizienz von elektrischen Antrieben in Bahn- und Busanwendungen. Hierbei werden metallische Gehäusekomponenten eines Traktionsmotors durch maßgeschneiderte Faserverbundtechnologien ersetzt, wodurch ein leichter, leistungsstärkerer und geräuschärmerer Motor entsteht.
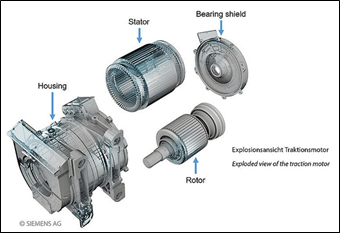
Abbildung 2: drivEcomp II: Explosionsansicht Traktionsmotor
Das branchenübergreifende Projekt „Next-Move“ in Kooperation mit Airbus, Liebherr und weiteren Projektpartnern bildet einen Einstieg in eine neue Herstellungsmethodik, die die Produktion von geschlossenen Hohlstrukturen auf effiziente Art ermöglicht und neue Freiheiten bei der Konstruktion eröffnet.
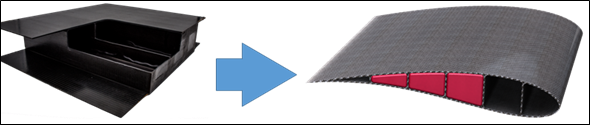
Abbildung 3: Next-Move: Herstellung von komplexen Hohlbauteilen (z.B. Landeklappen) mit Hilfe von strukturellen Kernen (CFK-Hohlkörper)
Unter der Leitung von Airbus und mit Partnern aus der Luftfahrt arbeitet das IVW seit November 2022 an der Entwicklung von integralen Bauweisen, Simulationsmethoden und Herstellprozessen für thermoplastische Rumpfkomponenten der Zukunft. Die wesentliche Innovation seitens des IVW liegt in der Entwicklung der geschlossenen Kette aus Bauteildesign, Prozesssimulation und Herstellprozessentwicklung inklusive der Validierung der Bauweisen und Prozesse. Die neuartige Bauweise der Türumgebung birgt einerseits hohes Leichtbaupotenzial und andererseits Kosteneffizienz durch die Kombination von schnellem Tape-Legen und nachgeschaltetem Thermoformprozess. Auch die simulative Auslegung des Herstellprozesses für thermoplastischen Profile ermöglicht einen Qualitätssprung. Durch den Einsatz ressourcenschonender Prozesse mit geringem Energieverbrauch und minimiertem Verschnitt bietet die Herstellung der Bauteile mit thermoplastischem Material außerdem einen positiven Einfluss auf den ökologischen Fußabdruck. Darüber hinaus bietet die Digitalisierung der Prozesse vielfältige Ansätze zur Reduktion von Ausschuss, Energiebedarf, Tests und Prüfungen.
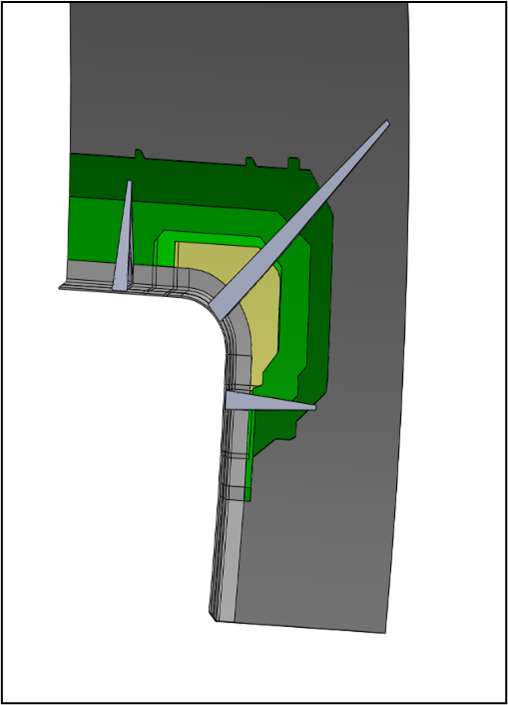
Abbildung 4: ZEUS: Entwicklung einer integralen thermoplastischen Türumgebung für ein Verkehrsflugzeug
Auch ist das IVW aktuell mit dem CVC im vom Bundesministerium für Wirtschaft und Klimaschutz geförderten Verbundvorhaben »WaVe« aktiv. Ziel des Vorhabens ist ein wasserstoffbasiertes Antriebssystem für Nutzfahrzeuge im Medium-Duty-Bereich zu entwickeln und anhand verschiedener Demonstratoren in Feldversuchen zu erproben. Im Rahmen von »WaVe« entwickelt das Leibniz-Institut für Verbundwerkstoffe mit seinen Partnern das Tanksystem für gasförmigen Wasserstoff.
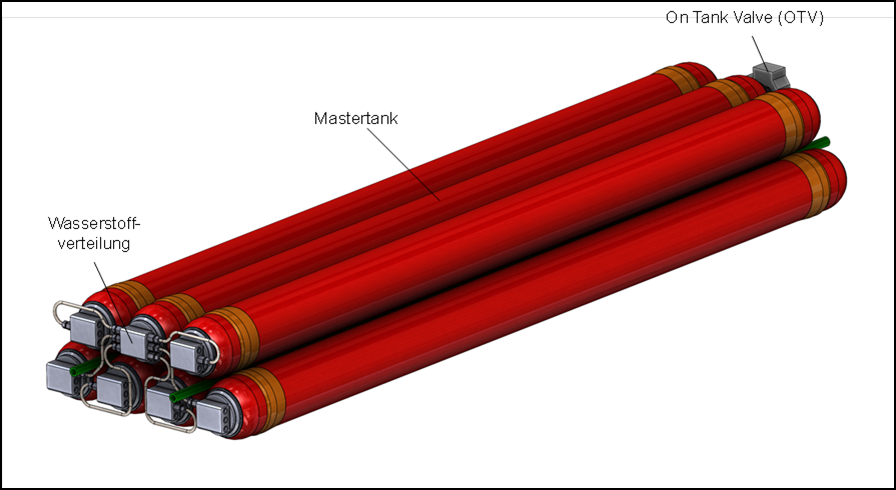
Abbildung 5: »WaVe«: 7-er Tankmodul zur gasförmigen Wasserstoffspeicherung für optimale Bauraumausnutzung
Allen Anwendungen voran steht die Werkstoffcharakterisierung, um Bauteile optimal auslegen zu können. Hierfür arbeitet das IVW in Forschungsprojekten sowie Arbeitskreisen (z.B. DIN, ISO, AVK, u.a.) an der Entwicklung neuer Charakterisierungsmethoden von thermoplastbasierten Faserkunststoffverbunden sowie deren Standardisierung. Ein wichtiger Bestandteil dieser Arbeit ist auch die Virtualisierung der Werkstoffe durch Simulations- und Materialmodelle. Dabei soll ein Verständnis der komplexen Zusammenhänge innerhalb eines Werkstoffes generiert werden, um die Materialeigenschaften optimal an die Anwendungsbedingungen anzupassen. Außerdem wird somit eine kosten- und zeitreduzierte Vorhersage des Materialversagens auch bei komplexen Geometrien und/oder Randbedingungen ermöglicht, wodurch potentielle Schwachstellen oder Probleme frühzeitig erkannt werden können, was besonders in den Bereichen Luft- und Raumfahrt sowie Automobilindustrie relevant ist, da hier hohe Anforderungen an die Zuverlässigkeit und Sicherheit von Materialien gestellt werden.
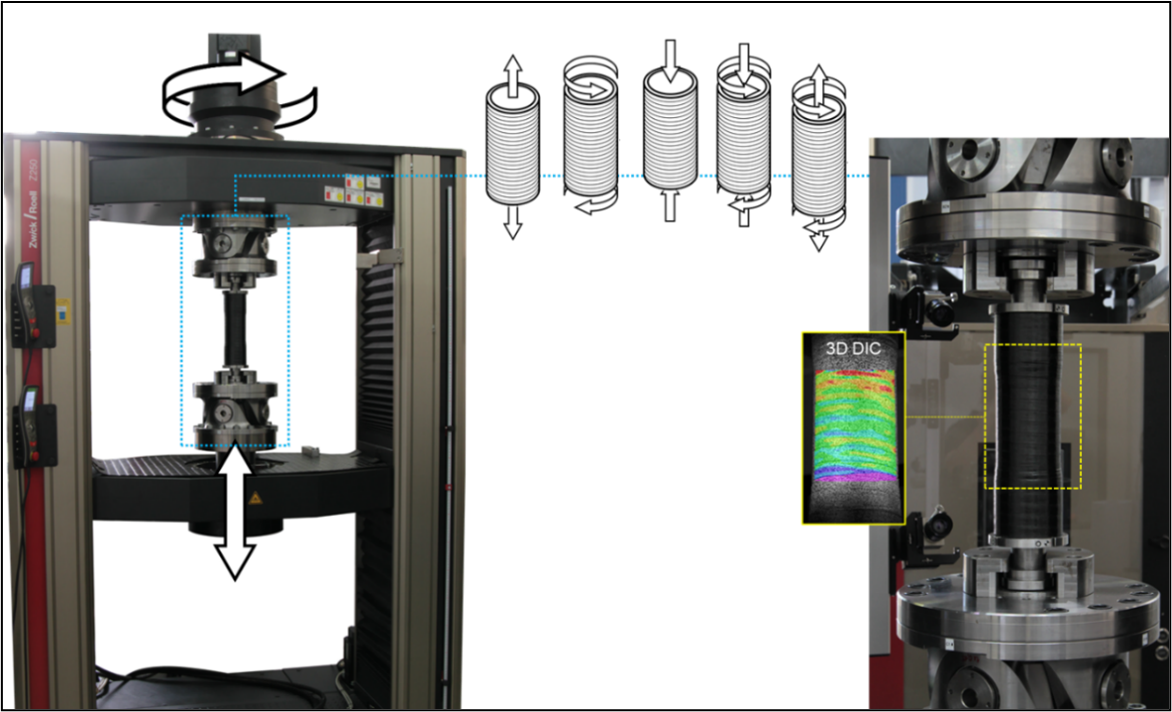
Abbildung 6: Gewickelte Rohrprobe in Zug-Druck-Torsions-Prüfmaschine
Zusammenfassend lässt sich sagen, dass nicht nur für die Mobilität, sondern auch für die Bereiche Energie, Klima und Umwelt, Produktionstechnologie und Gesundheitswesen die Tätigkeiten des IVW von großer Bedeutung sind. Mit seinen Forschungs- und Entwicklungsarbeiten geht das Leibniz-Institut für Verbundwerkstoffe in Rheinland-Pfalz als Best Practice Beispiel voran.